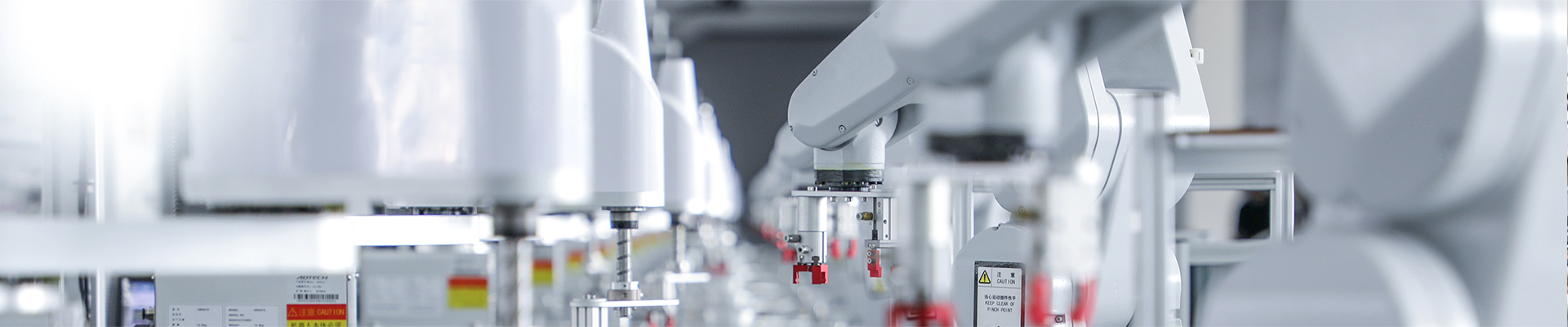
What are the best practices for managing conductor clearances and ensuring safety during OPGW stringing, especially when working near energized lines or crossings?
2025-07-19OPGW stringing inherently involves working at height and often near existing energized power lines, making conductor clearance management and safety paramount. Adhering to strict best practices is essential to protect personnel, prevent damage to existing infrastructure, and avoid catastrophic incidents.
I. Critical Safety Protocols & Planning:
-
1. Comprehensive Pre-Stringing Survey and Risk Assessment (Job Hazard Analysis - JHA):
-
Best Practice: Conduct a detailed site survey to identify all existing utilities, crossing points (roads, railways, power lines, communication lines), and potential obstacles. Perform a thorough JHA to identify all hazards and develop specific mitigation strategies for each span.
-
Implication: Our expertise extends to advising on meticulous planning, including identifying suitable puller/tensioner sites and intermediate setup points.
-
-
2. De-energization (Preferred Method):
-
Best Practice: Whenever possible, and especially for work directly on or adjacent to conductors, de-energize and properly ground the existing power lines in the work area. Implement strict Lockout/Tagout (LOTO) procedures.
-
Implication: This is the safest approach and should be prioritized.
-
-
3. Minimum Approach Distances (MAD):
-
Best Practice: For work on or near energized lines, rigorously adhere to established Minimum Approach Distances (MAD) as defined by local regulations and utility standards. Only qualified and authorized personnel using approved insulated tools and equipment should approach within MAD.
-
Implication: Strict training and supervision are required.
-
-
4. Grounding and Bonding:
-
Best Practice: All stringing equipment (pullers, tensioners, reel stands), as well as tower structures and conductive parts of stringing blocks, must be properly grounded and bonded to the earth. This provides a safe path for any induced or fault currents.
-
Implication: Utilize high-quality grounding rods, clamps, and cables. Our equipment is designed with clear grounding points.
-
-
5. Warning Devices and Temporary Clearances:
-
Best Practice: At road crossings, railway crossings, or existing power line crossings, implement temporary warning devices such as:
-
Temporary Warning Structures/Nets: To prevent OPGW from sagging too low or contacting traffic.
-
Insulated Crossings Guards/Hoses: To protect existing energized conductors from accidental contact with the OPGW or pulling rope.
-
Flagmen/Traffic Control: To manage traffic flow and ensure public safety.
-
-
Implication: Requires careful coordination with local authorities (e.g., road, rail, other utilities).
-
-
6. Personal Protective Equipment (PPE):
-
Best Practice: Mandatory use of appropriate PPE for all personnel, including hard hats, safety glasses, high-visibility clothing, safety-toed boots, and insulated gloves/sleeves when working near energized parts.
-
-
7. Emergency Response Plan:
-
Best Practice: Develop and communicate a clear emergency response plan for potential incidents (e.g., accidental contact, equipment failure, injury).
-
II. Equipment and Methodological Considerations:
-
1. Pilot Rope and Running Boards:
-
Best Practice: Often, a non-conductive pilot rope is strung first, then a stronger pulling rope, and finally the OPGW. Running boards can be used for multi-line stringing to maintain separation.
-
-
2. Controlled Sag and Tension:
-
Best Practice: Maintain controlled sag and tension throughout the stringing process using precise pullers and tensioners to prevent unexpected contact with obstacles or existing lines.
-
-
3. Continuous Communication:
-
Best Practice: Maintain constant, clear two-way communication (e.g., radios, headsets) between all personnel involved in the stringing operation – puller operator, tensioner operator, tower crews, and safety officers.
-
-
4. Spotters and Safety Observers:
-
Best Practice: Designate dedicated spotters at critical points (crossings, close proximity to other lines) to continuously monitor clearances and provide immediate warnings.
-
-
5. Weather Monitoring:
-
Best Practice: Monitor weather conditions closely (wind speed, lightning risk). High winds can make controlled stringing impossible and increase the risk of conductor swing. Suspend operations during adverse weather.
-
Our comprehensive OPGW stringing solutions include not only the highly controllable stringing equipment but also guidance on best safety practices and a range of safety accessories, helping our clients execute challenging OPGW installations with the utmost safety and precision.